Indian Railways is constantly striving to give quality inputs towards Electric Locomotive Manufacturing and Maintenance.This blog helps discussion in same.Email me indiwindy@gmail.com.
Wednesday, September 28, 2016
Monday, September 26, 2016
Saturday, July 23, 2016
Loco final inspections
Problem
of defective CBC lock pin was observed in the outgoing locos.
This
lock pin (trade item) does not have head-protrusion.
CEE(P&I)
inspected roof of TP-44 alongwith CEE(Loco) and Shell production staff and inspection staff.
Necessary
instructions were given to inspection staff for checking the same.
Paint
thickness measurement in the outgoing locos was also carried out by
CEE(P&I).
In
the out going loco, air was leaking
through TM blower.
Inspection
staff was instructed to generate NC for same.
Problem
of WAP5 gasket-roof was analysed in the shop today.
Fixture
for drain channel. Calibration needs to be checked.
Camber
for the roof arch is checked regularly as seen in the records.

It
is also suspected that stacking of one roof over other ( WAP5 sheet is thinner
than other locos) either in Shop#12 or in Shop # 16 might have deformed the
profile which results in gap between roof and the gasket.
Drain
Channel Panto roof.
During
inspection of a loco in Bay#2 ,it was found that RSPS cowl was not having 2
bolts , which was due to non-matching of
holes.
Thursday, July 21, 2016
Whats latest in Indian Locomotives
Silent Engines:
Code of federal practice 49, Pt 229.121a limits noise inside loco cab to 85 Db.
In 3 Phase its < 85 Db at present but in Conventional its near or > 90 Db.
RDSO Modification sheet # 448 issued in this regard.
Reliable Traction Motor Support :
RDSO Modification sheet # 447 Rev 0 issued in this regard.
RDSO SMI No. 0269, Rev. 1
12 mm safety sling IS : 2266 Garde 1770.
1810 mm for TM 3 and 4
1510 mm long for TM 1, 2,5 and 6
Sling has D shackles on both sides. as per IS : 2415-2004 Grade 8
Standardisation of safety sling for compressors:
For 3 phase locos
RDSO SMI No. 0242, Rev. 1 issued.
8mm dia wire rope. as per IS 2762-2004 grade 1770
High reach panto:
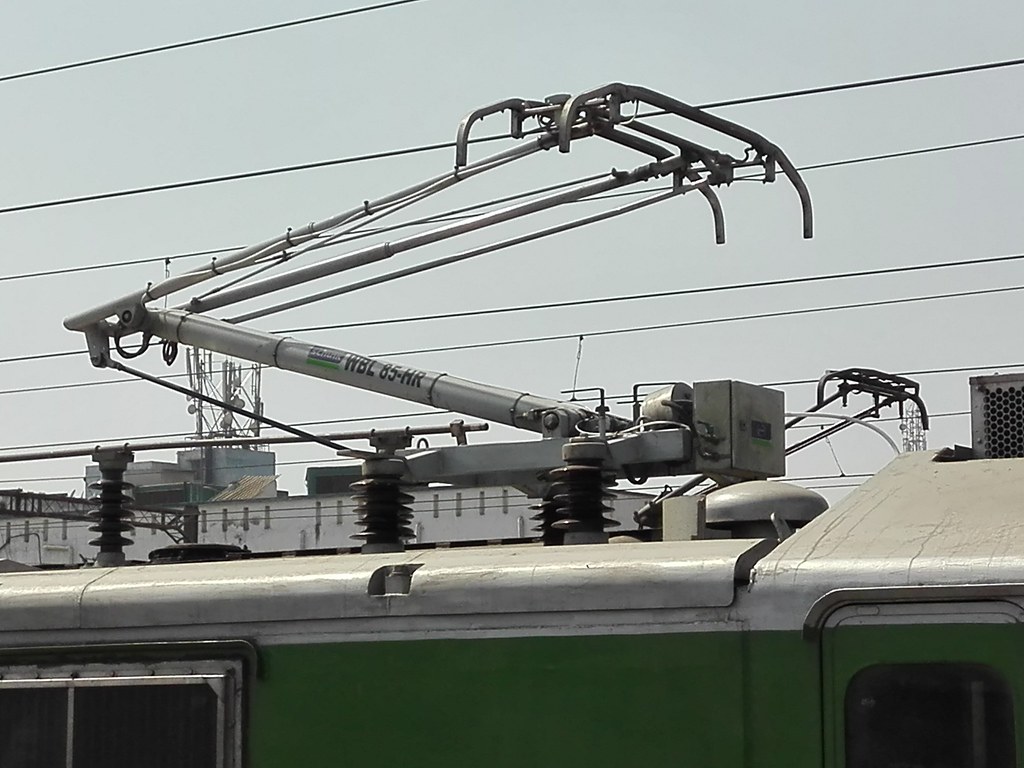
To overcome:
Better bearing maintenance:
Code of federal practice 49, Pt 229.121a limits noise inside loco cab to 85 Db.
In 3 Phase its < 85 Db at present but in Conventional its near or > 90 Db.
RDSO Modification sheet # 448 issued in this regard.
Reliable Traction Motor Support :
RDSO Modification sheet # 447 Rev 0 issued in this regard.
12 mm safety sling IS : 2266 Garde 1770.
1810 mm for TM 3 and 4
1510 mm long for TM 1, 2,5 and 6
Sling has D shackles on both sides. as per IS : 2415-2004 Grade 8
Standardisation of safety sling for compressors:
For 3 phase locos
RDSO SMI No. 0242, Rev. 1 issued.
8mm dia wire rope. as per IS 2762-2004 grade 1770
High reach panto:
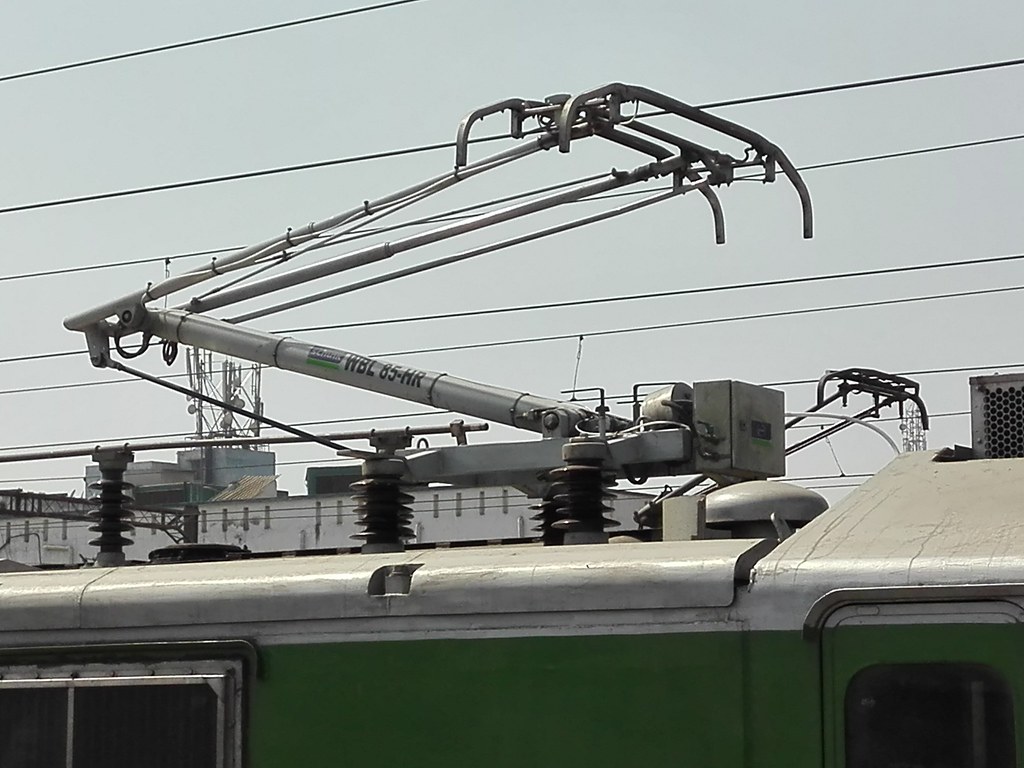
WBL -85
- Can be fitted even in WAP4 ( due to DBR problem) with base as 1900 mm
- Air bellow operated
- Less no. of components.
- fit for 200 kmph
- Has Auto Droppping Device
- Has over-reach detection device.
- 2030 mm panto pan ( 230 mm extra )
Better CCB ( computerised control break ):
To prevent following failures:
To prevent following failures:
- Air leak from BPCB valve
- Air leak from unloader valve
- Breakage of AFI guage glass
To overcome:
- Provide Wire Mesh Filter
- Dirt collecter at CCB panel
- BP pressure at ze
- ro before attachment, 5 Kg after BP FP coupling.
- Improving rubber seating quality by VITON
- AFI glass thicness increasefrom 8 mm to 12 mm
Better bearing maintenance:
- Follow FIFA strictly
- Fix assembly component ij kit form
- Measuring radial clearance as per SMI-278
- Induction heatng of seating of MSU bearing.
- Adequate stock of TM and MSU bearing and grease.
- Temp controller and demagnatising feature in induction heater.
- Color matching of pinion as per SMI-278
Wednesday, July 20, 2016
Quality Inspection
Pantograph
section was inspected .
AM92
AM 12
Since
Erode shed reported failure of MVMT, same was inspected in the shop.
MVMT(
TM cooling blower motor) is trade item and inspected for correct direction of
running, abnormal sound if any.
Failure
was reported in Loco no 22877( WAP5 ) by Santaraganchi shed . Triplate copper
pipe failure ( Stone India) was discussed in shop floor.
It
was noted that TRIPLATE was a trade item, fitment of the copper pipes was done
in shop only.
Quality Inspection
Stator
of 3-phase motors were stacked without any cover. Production staff were
instructed to cover for preventing dust ingress.
Modified
inspection cover was inspected in Hitachi TM. It is part of RDSO (modification
MS N0 0364).
Copper
pipe failure as reported in the loco #
22864 was analysed.
It
was reported that copper pipes cracked while hot bending. Cold bending is not always
possible. Although copper pipes have passed chemical tests in CLW lab, quality check must continue.
Subscribe to:
Posts (Atom)